Forced induction has been around for a while and is a very important part of modern automotive culture. Whether it be super- or turbocharging, air is drawn in from the atmosphere and forced into the engine by means of a compressor or pump. The result is an engine which makes more power than it could with natural aspiration, since each cylinder is filled with more air than it would be able to draw in by itself. Forced induction is especially useful on small displacement engines, because power is increased while maintaining higher fuel efficiency. There are several important parts to a turbocharging system you should get to know, and each has an equally important job to do in order to make the system operate properly. Today, we’re going to get to know the intercooler just a little better.
The Science of Boost
You surely know the basics by now: exhaust gasses leave the engine to spin a turbine wheel. The turbine is attached to a shaft, and on the other end is a compressor wheel which draws in air from the atmosphere, compresses it, and forces the pressurized air toward the engine. In some applications, there is a wastegate which controls how much exhaust is allowed to move the turbine wheel, and on a gas engine there is a blow off valve which diverts the compressed air around the throttle blade when it suddenly closes upon deceleration. Overall a turbocharging system is very simple, but there is one important law of physics which we cannot forget about, and that has to do thermodynamics.
While the math behind it all is very complicated, the concept can be summed up easily: whenever you compress a gas (like air), its temperature will increase. Additionally, whenever the temperature of a gas rises, its density goes down, and in the case of an internal combustion engine, less dense air can contain fewer molecules of fuel, and the resulting mixture will generate less power. For some real-world numbers, the temperature of the air leaving the turbocharger can sometimes be as warm as 300˚F, but for optimal power and efficiency, you want the air entering the engine to be as close to atmospheric temperature as possible. This problem is well understood by the OEMs, and early designers knew there had to be a way to lower the temperature of the air coming out of a turbo, and the solution engineers came up with is the intercooler.
Air to Air: A2A
There are two main types, but the function is more or less the same: in order to remove excess heat, the charge air is forced through a radiator-like device which has hundreds of tiny passageways which exponentially increases the surface area the air touches, and the core is made from a thermally conductive material like aluminum. The heat from the compressed air is quickly transferred into the core. To pull the heat out of the core, you have two methods of transfer: air or water. The most commonly used style of charge air cooler is classified as air to air, because it simply uses outside air to cool down the core just like with a radiator, trans cooler, or A/C condensor. Usually, the intercooler is on front of the vehicle right behind the grille, and is mounted in front of any other radiators or heat exchangers. Almost every single diesel engine on the road today uses an air to air intercooler, and in pickup applications, it started around 1991 when the VE Cummins added an intercooler, and you can still find them today on just about every diesel truck, with the exception of the 6.7 Powerstroke.
Air to Water: A2W
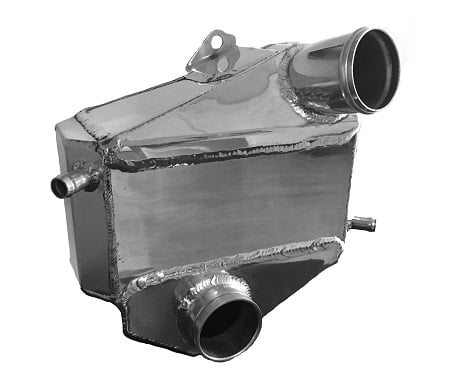
While an air to air system is inexpensive to manufacture, simple to plumb, and almost never fails, it does require a fair amount of real estate in front of your cooling stack. If space on the front of a vehicle is at a premium, sometime an air to water intercooler system is employed, but it is a bit more complicated. Hot air from the turbocharger is pumped through a heat exchanger, and the heat is transferred from the air into the core. Water is circulated through the other side of the core to remove the heat, but now you have a bunch of hot water you have to deal with, so the water is circulated with a small electric pump to the front of the vehicle and into another, more compact heat exchanger (known as an LTR or low temp radiator), where fresh air takes away the heat from the water. The chilled water goes back around to the primary heat exchanger to get warmed up again and pull more heat away from the charge air. As you can see, there is a lot more going on with an air to water intercooler system. You have coolant lines, an electric pump, a reservoir and expansion tank, and of course the low temperature radiator, not to mention the electronics to control it all like relays and sensors. The biggest benefit to an air to water system is liquid has a thermal conductivity about 23 times greater than that of air, so the intercooler in question can be a lot smaller and mounted in a tighter spot.
So, What?
Now that we’ve covered the fundamentals of intercooling, what does this all mean to a diesel truck owner in the real world? Like we already mentioned, every truck made this century has an intercooler from the factory, so you should be able to turn up the boost, add a lot more power, and go racing, correct? Not so fast…
I’ve hit on this concept time and time again, and it applies to intercoolers as well: any time you add power to your engine, you need to adjust every component which is part of the power generating system in equal proportions, and if you forget about the intercooler, there are several ways it can be pushed to its limit. First, is thermal efficiency: once you turn up the power, you are working the turbocharger harder which generates more heat, but there is a limit of how much heat the core can reject at any given time, and if you exceeded the limit, the air entering your engine will be hotter, less dense, and your power output will fall off, even though you’re making more boost. (Remember: power is made with air density, not just boost pressure.) Next, you have pressure drop. There is a limit to how much volume of air can flow through a core, and the stock intercoolers are well matched to a stock turbo and power level. If you increase the airflow with a larger turbocharger or compounds, the air passing through the core can wind up in a traffic jam of sorts. More air is being pushed into the intercooler, but only so much can come out. And finally, there is a limit to how much pressure the structure can physically hold, and in extreme cases where boost pressure exceeds 100psi you can split a stock aluminum intercooler open. For some trucks the failure threshold is much lower, especially if you have an oddball like the LMM Duramax or the one year only 2005 Ram which use plastic end tanks. For all those reasons and more, every performance diesel build should have an upgraded intercooler.
Bigger and Better…
Banks Power has been making diesel performance parts arguably longer than anyone else, and they take a very scientific and data driven approach to developing parts which improve the performance of your diesel, so you know they’ll live up to their claims. Whether you have an earlier model diesel truck which came from the factory without an intercooler, or you’re increasing the performance of your later model rig, a Technicooler System will work much better than any factory parts. The LLY Duramax for example was intercooled from the factory, but the truck suffered from overheating issues for a variety of reasons, but the heart of the problem is heat generated from combustion. While a less restrictive LBZ style turbo inlet goes a long way to keeping coolant temps low, upgrading to a Banks Technicooler system will aggressively increase the cooling capacity of the LLY. In this case, it has a 25% larger core and will flow 34% more volume of air, plus its constructed entirely from high strength aluminum which eliminates the possibility of cracking, and the Technicooler system also comes with larger 3” charge air tubes to further increase airflow. Altogether more heat is removed from the compressed air, combustion and exhaust temps go down, fuel efficiency goes up, and your engines coolant temp will also go down, especially in a constant-power scenario like towing a heavy trailer up a mountain pass, which is where the LLY has the most trouble.
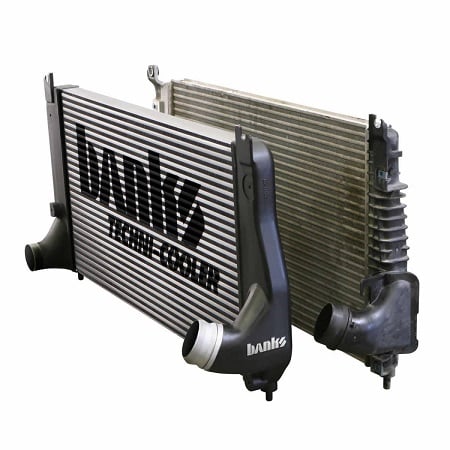
The 1994-97 7.3 Powerstroke, 1989-1991 5.9 Cummins, and early GM 6.5 trucks were all turbocharged yet had no intercooler. Power output from those engines wasn’t great to begin with, and perhaps this is why the designers didn’t see fit to add an intercooler, but it’s kind of like shooting yourself in the foot since the lack of an intercooler can limit power production. When you are working your truck near its limit, the air temperature at the exit of the compressor can be as high as 300˚F which is less than ideal for fuel mileage or horsepower. We already know the answer to this problem is adding an intercooler, but normally on an older vehicle you’ll have to get creative with your welder and some fab tools to mount an intercooler, but Banks once again can come to the rescue. For the OBS Powerstroke guys, you can install a properly engineered intercooler kit with basic hand tools and no fab work, and in a weekend, the Technicooler System will give your 7.3 all the benefits of a high-performance intercooler, which should’ve been on the truck to begin with.
There has only been one pickup built so far which came equipped with a water to air intercooler system, and that distinction goes to the 6.7 Powerstroke. The primary heat exchanger sits low on the driver’s side of the engine bay behind the headlamp, and the low temp radiator sits behind the grille in the usual spot. Unfortunately, the stock intercooler has been known to fail internally, and cracks form between the air and water sides of the core, which is bad news since that means coolant can now be pushed into the engine. Not only can the core crack, when increasing performance, the stock intercooler is an airflow restriction as well. Mishimoto has developed a cure for both issues, by designing a much stronger and more efficient bar-and-plate style core. The end tanks are made from cast aluminum, and the whole thing is precision TIG welded together. Once installed under the hood of your Superduty, airflow is increased by 22%, and dyno tests show by simply swapping out the intercooler, you can see this a gain of 40 pounds of torque with no additional changes required.
Meth Is Bad for You…
If you have limited space for an intercooler, or just have problem with higher EGTs, there is one more way to help out without physically altering the size of the intercooler, and that’s with a chemical spray. It may sound absurd, but by injecting a precise amount of 50/50 water and methanol blend into the intake stream right before it enters the engine, you will see the exact same effects as an intercooler. AEM Electronics has a kit which includes everything you need to install water methanol injection onto your diesel, including the reservoir, pump, high pressure hoses, nozzle, and of course the electronic control unit. Once its installed, you’ll have a gain in horsepower, increased fuel efficiency, lower air temperature, and even a reduction in particulate matter.
Keep Your Cool
The simple fact of the matter is any turbodiesel engine ought to have an intercooler, and the bigger the better. While it is primarily responsible for keeping the IAT of the engine low, you help the intercooler out by creating airflow efficiency in other areas of the engine, like using a cold air intake, high flow exhaust manifolds and up-pipes, down pipe, good tuning, and a free flowing exhaust. It’s just like being in high-school algebra: remember to balance those equations!
The information in the 2nd paragraph of “The Science of Boost” contains inaccuracies.
The explanation of the “less dense air containing fewer molecules of fuel” is not correct. The pretense requirement of burning oxygen is missing. The method of thinking should always be that the goal to making power is bringing in as much oxygen as possible: you can always dump in more fuel, but the challenge to making power in any application is getting the highest number of oxygen molecules as possible for each combustion cycle. The chemical reaction of combustion requires 3 components: oxygen, fuel, and an event that triggers the ignition of those two. The oxygen vs. fuel requirements are a specific ratio (air/fuel ratio) for the chemical reaction to be perfect, so if you have a less dense air charge (and therefore less oxygen for a given volume), you require less fuel to burn to achieve stoichiometric perfection.
“Wanting the air as close to atmospheric temperature as possible” is the only goal for those who simply want to bolt on an intercooler and run. But the ultimate goal to making power is getting the intake air temperature as low as you can get it. Many big power guys run an air to water intercooler with an ice box, and when they are done with a drag run, a pull, dyno run, etc. they have been pulling air in so cold that condensation actually formed on their plumbing and manifold. They understand that if they want more power they need more oxygen and the more the air is cooled, the more dense the air will be, and in turn there will be more oxygen available to burn. Keep in mind that to keep the chemical equation balanced (stoichiometric), you will need to add fuel as you increase the oxygen density.
Both great points and thank you for taking the time to read.
Point 1: In an attempt to not be too technical or long winded, I did skip over the concept of air/fuel ratio and ideal stoichiometry, since that’s a whole conversation on its own. Perhaps a more accurate, but still concise, way to write the sentence in question would be: Additionally, whenever the temperature of a gas rises, its density goes down, and in the case of an internal combustion engine, less dense air contains fewer molecules oxygen, and if the ratio of air to fuel remains the same, the resulting warmer mixture will generate less power.
Point 2: Also correct. There are many racers who use ice or even tie into their A/C system to chill their intercooler well below ambient temperature, but I was writing this article based on the premise of a street driven truck. Those systems have to be filled with ice before every run, and then you have to drain out all the melted ice afterwards to replace with more ice for the next run. Yes, the ice-cold air will have the capacity to make a lot more power (when mixed with the correct amount of fuel), but its not necessarily the most practical for a daily driver or a tow rig, which is how the majority of diesel owners use their trucks. It is a point worth mentioning however.